Share this
Battery configurations in data centers
by PowerShield on Nov 13, 2017 11:44:00 AM
This is the second in a series of units that will educate the reader on the part played by a battery in an uninterruptible power system (UPS).
Battery types
In our introductory unit we pointed out that lead-acid batteries are the preferred method of energy storage for UPS systems in about 95% of all data center applications. We also stated that lead-acid batteries can be split into two main categories or technology types: valve-regulated or vented.
Before getting into the technical details of each technology, it is important that we are clear on two terms:
- cell: A cell is the basic electrochemical building block of a battery. It is in a container (sometimes referred to by the slang term “jar”) holding positive electrodes, negative electrodes, and electrolyte. A container can be single-cell or multi-cell. For example, a common 12-volt battery unit contains six 2-volt cells in series inside a single container. The “battery” manufacturer’s specifications apply only to cell units.
- battery: A battery is one or more cells connected in series, parallel, or both, to provide the required operating voltage and current levels required by the load equipment. In other words, the user or integrator assembles the cells (frequently at the owner’s site) to create a battery. A UPS battery can consist of dozens or even hundreds of cells.
Valve-regulated lead-acid (VRLA) cell -- VRLA is the technology of choice in the majority of UPS applications for a number of reasons:
- “Sealed” construction - The VRLA cell is usually sealed, so it does not release flammable hydrogen gas and oxygen under conditions of normal use. As the name implies, it has a “valve” that can open and release gas when internal pressure exceeds a specified level such as under fault conditions. This means that the ventilation requirements are not as rigid as they are for vented lead-acid cells (discussed below)
- “Reduced maintenance - Because the cell container is opaque, visual inspection of liquid levels is not required. Likewise, it is not necessary to periodically add liquid to the electrolyte. Gases created during electrolysis are recombined inside the cell rather than being released into the air.
- Immobilized electrolyte - VRLA has no free-flowing liquid electrolyte
- Smaller footprint - VRLA only holds about ten percent of the amount of electrolyte required in a comparably-rated vented cell. That makes the cells or multi-cell units quite a bit smaller.
- Easier assembly - Because the unit has no liquid electrolyte, it is possible to install VRLA units upright or sideways. VRLA batteries can be enclosed in a cabinet or on racks.
VRLA.trade-offs:
- Low temperature tolerance - High internal and ambient temperatures can accelerate the evaporation of electrolyte thereby leading to premature failure and/or overheating known as thermal runaway
- Shorter life - VRLA cells typically must be replaced more frequently than vented cells. Material, labor and recycling costs must be factored into the purchase decision.
Vented lead-acid (VLA) cell - Historically VLA’s were the preferred battery technology before the appearance of VRLA. As the name implies, the VLA vents continuously into the surrounding air. Some of the reasons for continued use of VLA’s, particularly in large (megawatt) applications, include:
- Longer life - The service life of VLA cells is typically last two to three times longer than VRLA.
- Greater visibility - Cell containers are transparent, so it is possible to visually inspect what is happening inside a cell and take corrective action such as adding more water to the electrolyte.
- Low risk of thermal runaway. Because of the high liquid electrolyte content, dry-out is unlikely with scheduled maintenance
VLA trade-offs:
- Battery rooms - VLA batteries can only be installed in dedicated rooms with ventilation systems that exhaust battery fumes to the outside of the building rather than circulate inside
- Large footprint - VLA cells are only installed upright on open battery racks. The installed footprint can be as much a twice that of VRLA
- Floor loading - VLA cells are mostly lead and liquid electrolyte, which makes them very heavy and difficult to install on the upper stories of buildings
- Spill hazard - Because of the large amount of liquid electrolyte in a VLA, spills and leaks are always a concern. The active ingredient in electrolyte is sulfuric acid, which is corrosive.
Installed form factor
As mentioned above, batteries can be installed in two configurations.
- Battery racks - Both VRLA and VLA can be installed on open racks that allow easy access for inspection and servicing. Racks are usually multi-tier or multi-step to reduce footprint. The trade-off is greater floor loading. Because of the potential of human contact with a dangerous electrical hazard, open racks must be in rooms only accessible by trained and authorized personnel.
- Battery cabinets - Only VRLA can be installed in cabinets. Because cabinets can have locked doors, the cabinets do not have to be in battery rooms; they can be installed directly adjacent to the UPS system and/or the information technology equipment. This eliminates the need for long dc cabling. Battery cabinets can be made to be indistinguishable from IT equipment cabinets. They must be properly ventilated to ensure no accumulation of hazardous gas.
To view the first unit in the series, click here. If you want to sign up to receive the following units as they are released, sign up to our newsletter here.
Share this
You May Also Like
These Related Stories
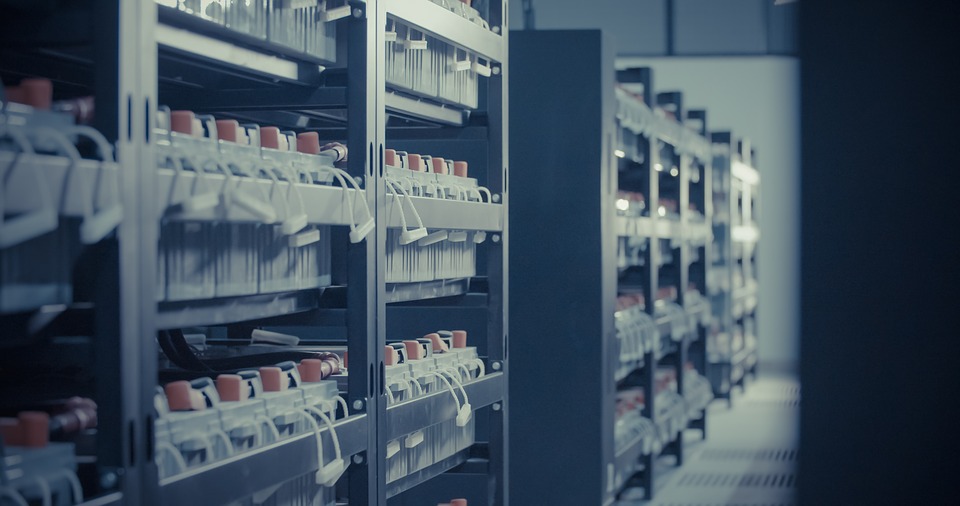
Battery charging regimes
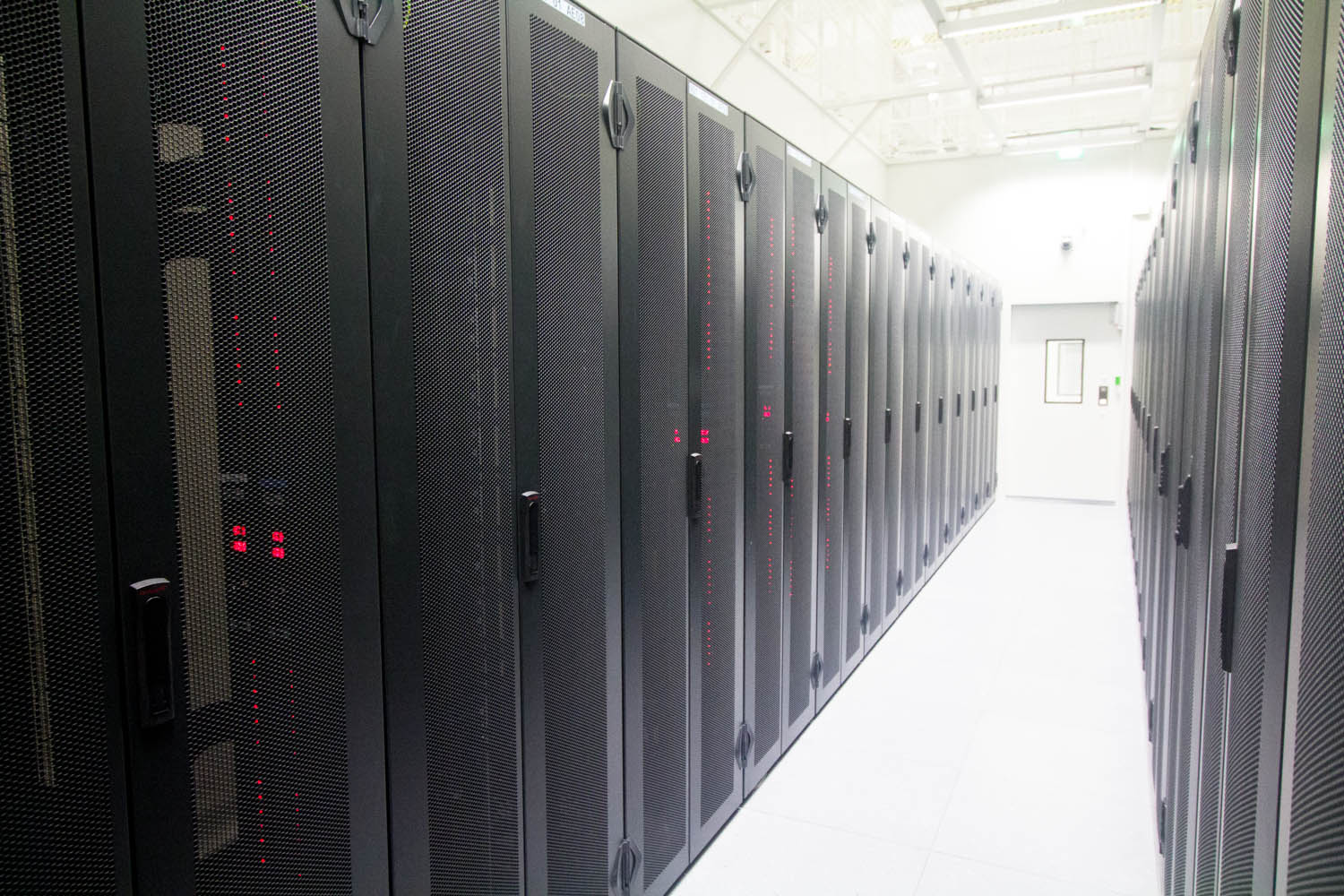
All things big and small
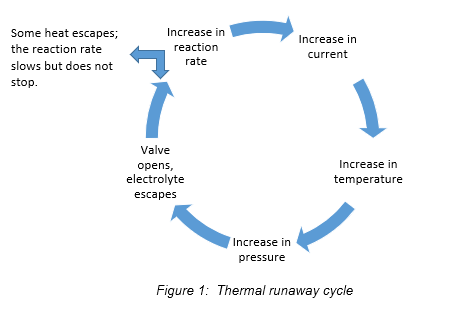
Thermal Runaway and Thermal Walkaway
- September 2024 (1)
- December 2021 (2)
- March 2020 (1)
- January 2020 (1)
- December 2019 (1)
- October 2019 (2)
- July 2019 (1)
- May 2019 (2)
- April 2019 (1)
- March 2019 (2)
- January 2019 (1)
- December 2018 (1)
- November 2018 (1)
- August 2018 (3)
- July 2018 (1)
- June 2018 (2)
- May 2018 (2)
- March 2018 (2)
- February 2018 (2)
- January 2018 (1)
- November 2017 (1)
- October 2017 (1)
- August 2017 (3)
- June 2017 (1)
- March 2017 (1)
- November 2016 (1)
- October 2016 (1)
- September 2016 (2)