Share this
Battery replacement intervals
by PowerShield on Jan 25, 2019 4:09:25 PM
This is the tenth in a series of units that will educate the reader on the part played by a battery in an uninterruptible power supply (UPS) system.
So you bought a battery with a nominal design life of “X” years. The realistic service life is actually significantly less than that, but you don’t know what it is. At around the “half-life” (i.e., half way through the design life) an individual cell-unit fails, then another. You replace the cell-units with new ones (maybe under depreciated warranty, or maybe at full price). Service technicians come in to replace the cells. Each visit costs money and disrupts the service while the work is being performed. You’re told that the new cells create an imbalance with the rest of the cells in the string. At some point you must decide that the entire battery string needs replacement. How do you know when that time has arrived? How do you know if your battery will be able to ride through the next power interruption?
Several factors must be considered, including:
- How many cells (or multi-cell units) are in the string?
- What has been the maintenance history of the battery?
- Has the battery been exposed to abnormal conditions, such as extreme heat?
- Are there other strings in parallel with this one?
- Do you have a monitoring system capable of taking ohmic measurements on individual cell-units?
- Do you have reliable records capable of comparing the current measurements to the original base-line measurements?
- What is the impact of “down time” when a battery or battery string is removed from service for cell replacement?
- What is the labor cost of cell replacement?
- How did the battery perform during the last discharge (or planned discharge test)?
A lead-acid cell or battery is considered to have reached “end of life” when it can deliver only 80% of its original capacity. A decision on “fix or replace” is very subjective. Generally speaking, when the number of cells needing replacement exceeds a certain percentage of the cells in the string, it’s time to replace the entire string. There is no formula that calculates all of these variables to come up with a magic number for what that percentage should be. Let’s look at some of the variables.
Number of cells in a string
In a telecommunications application with a 48-volt string consisting of four 12-volt units, one unit is 25% of the entire string. When one fails, it probably makes sense to replace the entire string. By contrast, in a UPS system with a nominal 480-volt string consisting of 240 two-volt units, it probably makes sense to replace a single failed cell. If the battery is fairly new, it’s possible that a single cell failure is an outlier, possibly due to factory defect. If the string has been in use for several years, one might conclude that if one cell goes bad, others may not be far behind. The user must make an arbitrary decision as to when too many cells or multi-cell units have failed or are expected to be near end-of life. That number should probably not exceed ten percent of the number of units in the string.
Maintenance history
If the battery has been well cared for, meaning that it has received regular preventive maintenance and has not been exposed to harsh environment, loss of a single unit might not justify replacing the entire battery. Good record keeping might have predicted an impending failure of a single cell as well as suggesting whether other cell failures are soon to follow.
Parallel strings
If the UPS battery system has redundant strings, such that the UPS can still function with one string removed (albeit with a shorter back-up time), full string replacement might be postponed. If the UPS has only a single string, taking the battery out of service for cell replacement (i.e., possibly requiring that the UPS be switched to bypass) puts the critical load at risk. The owner might decide that full replacement makes more sense than enduring multiple downtimes for remedial maintenance and cell replacement.
Monitoring system/record keeping
The importance of ohmic measurements cannot be overstated. Regular or continuous ohmic measurement allows real-time monitoring of every cell or multi-cell unit. By comparing the latest data from previous weeks or months, one can detect when a cell is aging faster than the average for the rest of the group. If a single outlier is detected, that unit can be replaced before it actually fails. If multiple cells appear to be significantly different from their original base line (e.g., 15% or more), the units should be watched more closely. If they continues to decline relative to their neighbors, it is probably time to replace the entire string. Consult the battery manufacturer for guidance based on the ohmic measurement method used.
Downtime
Although it is sometimes possible to bypass a single cell in a string while replacing it, this is a questionable procedure. Usually work on battery systems means removing the battery from the UPS during maintenance. One must consider the increased risk to the critical load. It may be necessary to schedule such work well in advance so that users can shift their work.
Labor cost
Although some large users have trained battery technicians on staff, most users must bring in qualified technicians, usually in a team. Such visits can be expensive, especially if they have not been budgeted. One must weigh the cost of such service against the value of the battery system. One or two visits might be tolerated. Beyond that, a cost/benefit analysis might suggest that it’s time for a new battery system.
Testing
In the first year of service one would expect the ohmic values of each cell to be reasonably consistent. As the battery ages, ohmic values may start to drift apart, some higher than others. That is normal and we usually look at the average. If one cell is significantly different, it may be a warning. Cells do not typically fail catastrophically over night, but they can age faster than their neighbors in a string. When too many cells get “out of whack,” it may be time to perform an equalize charge (see Unit 3 for a definition). [Note: equalize charge is not usually recommended for VRLA batteries; consult the battery manufacturer for guidance.] If the equalize charge fails to bring all the cells back into balance, the outlier(s) may be heading for premature failure. While ohmic measurements can identify the probability of early failure, the only way to know is to perform a discharge test. The discharge/charge cycle can have the same effect as an equalize charge. The discharge test can tell you the battery capacity at the time of the test. It cannot, however, guarantee the capacity on the next discharge. If the test reveals that the lead-acid battery is at or close to 85% of its original capacity, it is time to start budgeting for a battery replacement. Once it reaches 80% of rated capacity it should be replaced.
As stated earlier, a replacement decision is subjective and can only be made when all of the above considerations have been weighed for cost/benefit and risk assessment. What is the impact on -- and risk tolerance of -- the business for a battery failure? Every business will apply a different weight to each of the above considerations.
Share this
You May Also Like
These Related Stories
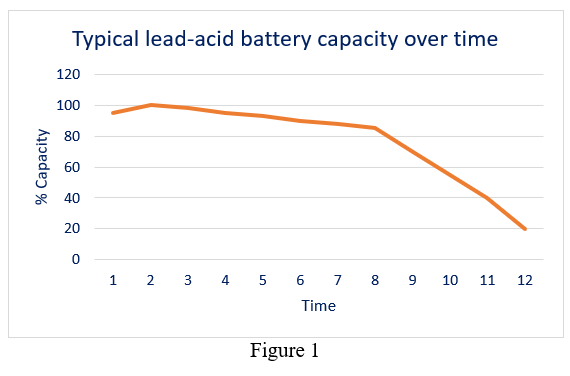
Monitoring VRLA State of Health
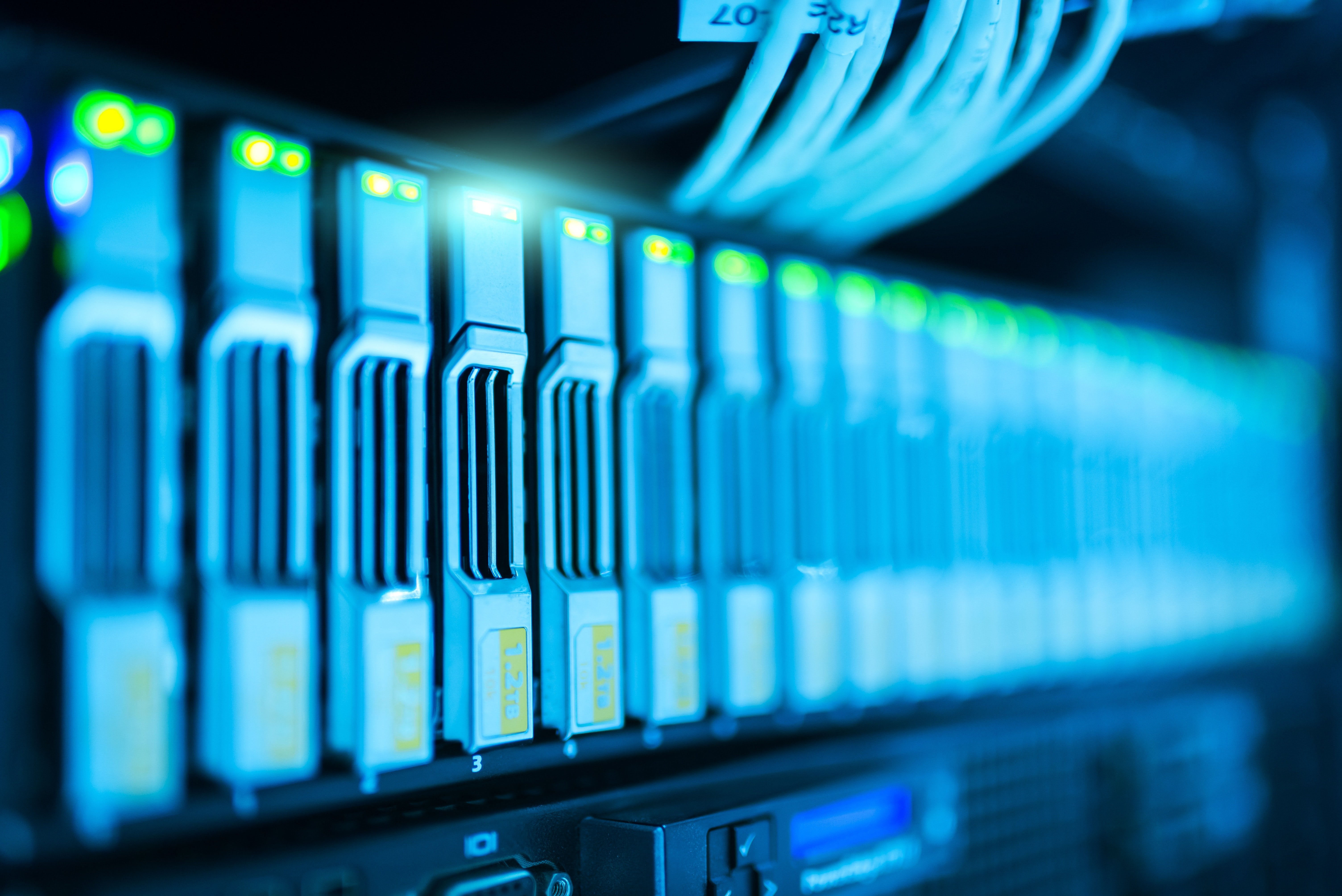
VRLA Installation and Commissioning
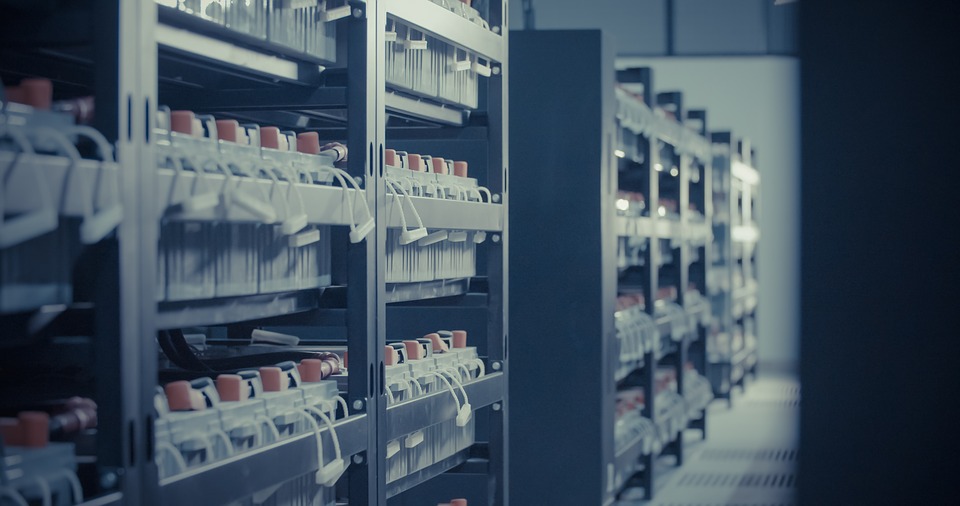
Speaking the language of batteries
- September 2024 (1)
- December 2021 (2)
- March 2020 (1)
- January 2020 (1)
- December 2019 (1)
- October 2019 (2)
- July 2019 (1)
- May 2019 (2)
- April 2019 (1)
- March 2019 (2)
- January 2019 (1)
- December 2018 (1)
- November 2018 (1)
- August 2018 (3)
- July 2018 (1)
- June 2018 (2)
- May 2018 (2)
- March 2018 (2)
- February 2018 (2)
- January 2018 (1)
- November 2017 (1)
- October 2017 (1)
- August 2017 (3)
- June 2017 (1)
- March 2017 (1)
- November 2016 (1)
- October 2016 (1)
- September 2016 (2)